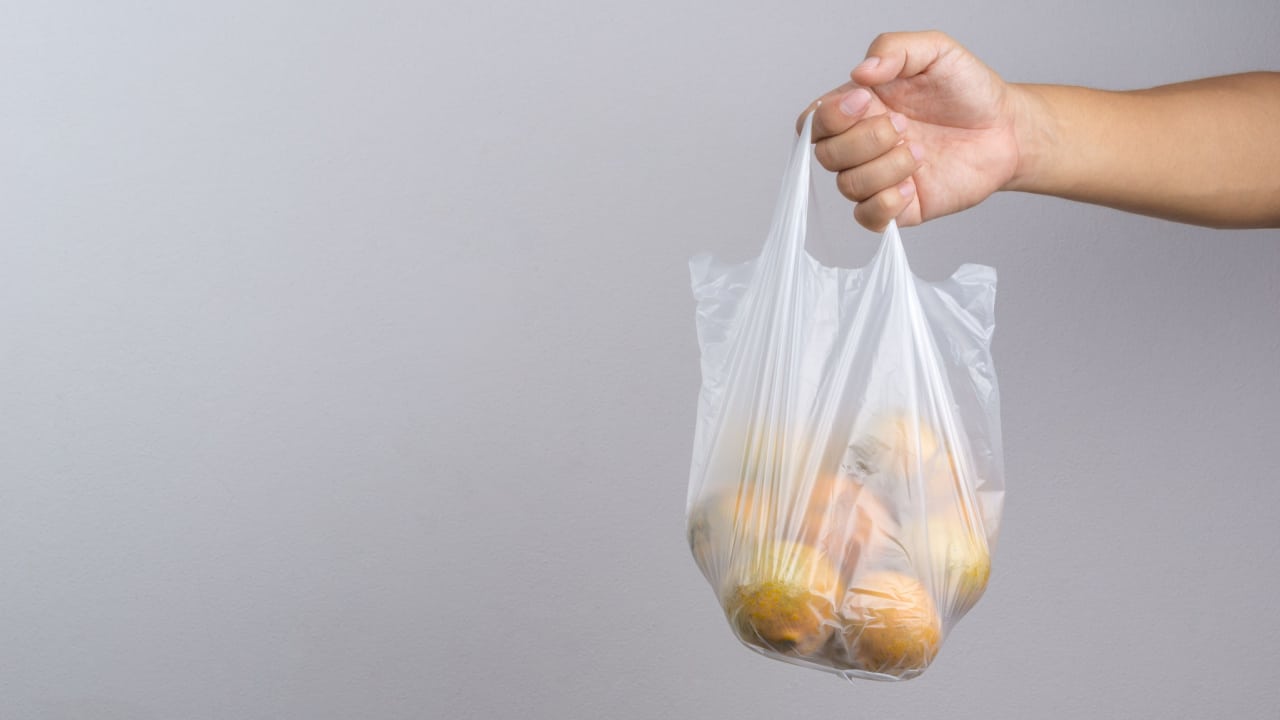
Desde o ano passado, estão saindo de uma fábrica em Curitiba resinas que servem de matéria-prima para embalagens plásticas que podem ir direto para o lixo orgânico, sem culpa. Elas se decompõem em até dois anos — uma fração dos séculos do plástico tradicional, feito a partir de derivados do petróleo. Se levadas à compostagem, viram adubo num prazo de até 180 dias.
A Earth Renewable Technologies (ERT) é a primeira empresa na América Latina a produzir resinas para plásticos biodegradáveis em escala industrial.
Com um investimento de R$ 50 milhões feito por clientes da XP Private em meados deste ano, a startup quer passar das atuais 3 mil toneladas de resinas por ano para 35 mil toneladas até 2025.
É um número ainda pequeno para as milhões de toneladas movimentadas pelo mercado de plástico.
Mas trata-se do primeiro salto de crescimento para um mercado que a empresa vê como exponencial, em meio a maior demanda de produtos sustentáveis por parte das empresas, aliada a uma vantagem comparativa relevante do Brasil neste ramo.
“O que a gente busca muito estando no Brasil é estar próximo da nossa matéria-prima, que é o açúcar, e realmente dar escalabilidade ao bioplástico”, afirma Kim Gurtensten Fabri, CEO da companhia.
Segundo dados da Bioplastic Magazine, que compila os dados do setor, hoje o mercado de bioplásticos movimenta cerca de US$ 10 bi, apenas 1,5% do total movimentado pela indústria do plástico em geral. A expectativa é que esse percentual passe para 6% em 2025 e 40% em 2030.
A categoria engloba desde os produtos compostáveis, como o da ERT, até aqueles de origem renovável, mas que tem como o melhor fim da vida a reciclagem. É o caso do plástico verde da Braskem, da marca I’m Green. Talvez o exemplo mais conhecido no mercado brasileiro, ele é obtido a partir do etanol, mas não é biodegradável.
Da prancheta à fábrica
A ERT foi fundada em 2008 por professores da Clemson University, da Carolina do Sul. Eles passaram quase dez anos desenvolvendo a tecnologia por trás dos plásticos compostáveis antes de lançar o produto no mercado.
A família de Fabri, que é tradicional no ramo imobiliário do Paraná, foi uma das primeiras investidoras, ainda na fase pré-operacional, quando os produtos estavam na prancheta (curiosidade: a modelo Gisele Bundchen também foi uma das primeiras a apostar na companhia). Foi apenas em 2019 que a empresa se tornou operacional, com a fábrica no Brasil.
O bioplástico da ERT é fabricado a partir do ácido lático obtido pela fermentação do açúcar. Um dos principais diferenciais da startup é conseguir fazer um bioplástico resistente e não quebradiço, que pode ser utilizado também em embalagens rígidas.
“Patenteamos toda a parte de reforço do bioplástico, o que dá funcionalidade para o plástico sem que ele perca a compostabilidade, sem adicionar nenhum componente químico ou plástico de origem fóssil”, diz Fabri.
A Puravida, marca brasileira de produtos alimentícios de origem natural que foi comprada neste ano pela Nestlé, foi uma das primeiras clientes da ERT e usa o material nos potes da sua linha de polivitamínicos.
Outro cliente é a Embalixo, de sacos e sacolas plásticas, que tem uma linha compostável voltada para armazenamento de lixo orgânico.
“Temos muitos projetos em desenvolvimento na área de cosméticos e de bens de consumo”, afirma Fabri.
Em teoria, todo o plástico é reciclável, mas a ERT mira principalmente os mercados em que a reciclabilidade é baixa.
Isso inclui as embalagens rígidas de polietileno de baixa densidade e polipropileno, que vão em frascos de shampoo e amaciante, por exemplo, e são o calcanhar de aquiles das metas de reciclagem das empresas de bens de consumo.
E também as embalagens flexíveis, como as usadas em salgadinhos e biscoitos por exemplo, e que acabam não chegando às recicladoras.
Restaurantes e empresas de delivery também estão entre os potenciais clientes. Isso porque as embalagens de papel e papelão de uso único para alimentos normalmente são revestidas de algum filme plástico — e o uso do bioplástico torna o produto efetivamente biodegradável.
Cerca de metade do faturamento da ERT vem de clientes brasileiros.
“Eu não tinha uma expectativa muito legal para o Brasil, sendo sincero, achava que não ia passar de uns 20%. Mas nesse ano fomos surpreendidos muito positivamente.”
A ERT vende diretamente para as fabricantes de embalagens, mas atua antes, na ponta, com o cliente, desenvolvendo as aplicações antes de levá-las para produção.
Verticalização
Com a tecnologia dominada, o custo é o maior obstáculo para a indústria ganhar escala, aponta o executivo. “Hoje, vemos um prêmio em cima das resinas de 1,8 a 3 vezes, dependendo da aplicação. E custo é um fator determinante para a indústria do plástico”, afirma Fabri.
O ácido lático utilizado na fabricação das resinas da ERT vem da Tailândia, que é um dos maiores produtores nesse setor.
Mas a empresa planeja avançar na cadeia para chegar à produção de matéria-prima no Brasil nos próximos anos.
“A companhia vê a verticalização como passo fundamental para a próxima etapa de crescimento”, diz o CEO.
Segundo ele, uma nova captação não está nos planos no curto prazo. “Ainda somos totalmente focados em investir, mas não pensamos numa nova rodada num futuro próximo. A nossa família controla a empresa. Não buscamos diluição e nem valuation maluco.”