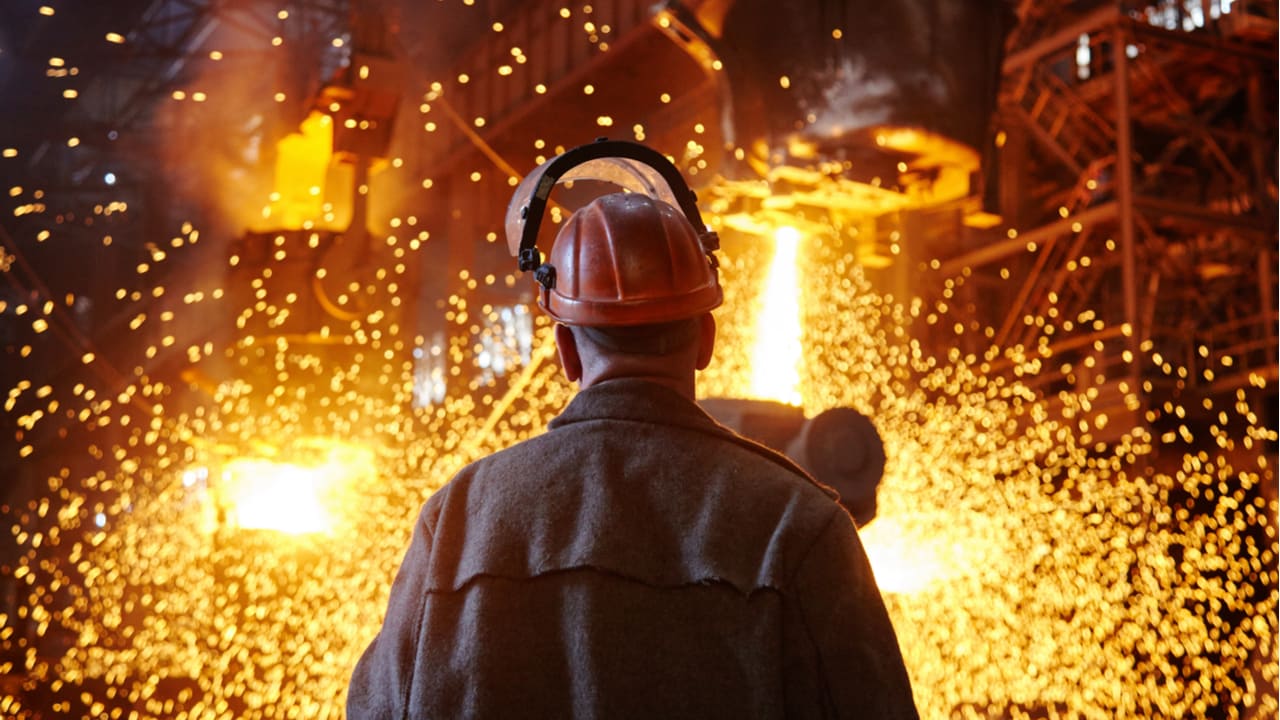
Pesquisadores da Universidade de Birmingham, na Inglaterra, desenvolveram um método para cortar em até 90% as emissões de CO2 das siderúrgicas. A tecnologia, que ainda precisa ser testada em escala, tem o atrativo de ser muito mais barata do que outras alternativas em desenvolvimento e, não por outro motivo, atraiu a atenção instantânea de empresas.
Utilizando cristais de perovskita, um material que tem o nióbio entre seus componentes, os pesquisadores criaram um sistema que recicla o próprio CO2 emitido na produção do aço e o transforma em uma fonte de energia.
“Basicamente estamos fechando o ciclo do carbono dentro do alto-forno”, diz ao Reset Harriet Kildahl, uma das autoras do paper, publicado no fim de janeiro.
A produção de aço é responsável por cerca de 8% dos gases de efeito estufa lançados na atmosfera, principalmente o dióxido de carbono, ou CO2, principal subproduto das usinas siderúrgicas.
A inovação proposta pelos pesquisadores envolve a construção de uma espécie de “unidade de filtragem” anexa ao alto-forno e alimentada pela chaminé.
Ao entrar em contato com a perovskita, as moléculas de CO2 são quebradas em duas: sobram um átomo de oxigênio e outro de CO, ou monóxido de carbono.
Esse CO pode ser então reinjetado no alto-forno para servir de combustível e reagir com o minério de ferro, substituindo até 90% do coque, ou carvão metalúrgico, usado no processo e altamente poluente.
A reação do cristal com o CO2 acontece a cerca de 800°C – o próprio calor do alto-forno, que pode atingir o dobro dessa temperatura, pode ser aproveitado.
Depois de “retirar” os átomos de oxigênio do CO2, o cristal pode ser reutilizado durante muito tempo. “Ele se autorrecicla”, diz Kildahl.
Caso comprovada em escalas maiores, a inovação tem implicações que vão além das reduções de emissões da siderurgia.
A mais imediata e importante delas tem a ver com o custo: além da economia com o coque, o método pode prolongar a vida útil das plantas baseadas em altos-fornos, responsáveis por cerca de 70% do aço produzido no mundo, o que reduziria drasticamente os investimentos na descarbonização do setor.
Os cristais de perovskita podem ter várias composições diferentes, dependendo da finalidade. Os usados no experimento britânico são produzidos artificialmente à base de cálcio e ferro, dois elementos baratos e amplamente disponíveis.
O terceiro ingrediente é o nióbio. Esse metal, que tem a maior produção no Brasil, é o único item de custo relevante, afirma Kildahl.
Já as alternativas em estudo para produzir aço de baixo carbono, como as que usam o hidrogênio verde, exigem investimentos bilionários para a construção de novas plantas.
Além disso, a produção de hidrogênio verde ainda está engatinhando no mundo todo. O preço desse vetor de energia ainda é proibitivo, e vai demorar mais de uma década até que os volumes sejam suficientes para atender à indústria do aço.
Outros métodos, como o de eletrólise desenvolvido pela Boston Metal, envolve uma maneira completamente nova de purificação do minério de ferro.
Corrida das empresas
Yulong Ding, co-autor do estudo e diretor do Centro de Armazenamento de Energia da Universidade de Birmingham, diz ter sido surpreendido pelo interesse da indústria desde a publicação do paper.
“Dissemos [às empresas] que o plano é ter uma planta piloto em cinco anos, e nos perguntam: ‘por que não acelerar esse prazo’”, afirma Ding.
Ele estima que essa primeira unidade vá consumir investimento de pelo menos 10 milhões de libras (cerca de US$ 12 milhões).
A ideia é formar um consórcio envolvendo empresas do setor para financiar o projeto e montar a primeira planta junto a um alto-forno pequeno e que esteja no fim de seu ciclo de vida.