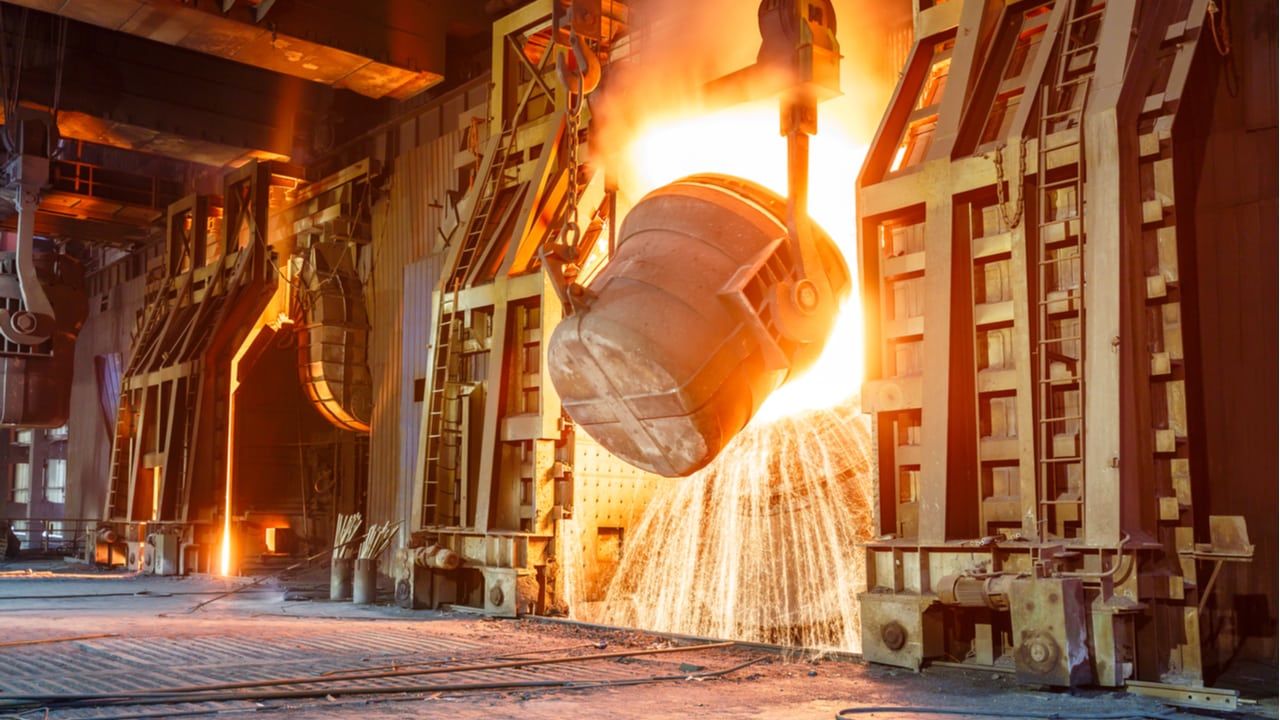
(Este texto foi publicado em primeira mão na newsletter Carbono Zero. Inscreva-se aqui.)
Existe um tipo de comentário que se ouve muito na época das COPs ou de qualquer outro grande evento ligado ao clima. É mais ou menos assim:
“Que beleza, todo mundo atravessando o mundo de avião para salvar o planeta.”
A contradição, claro, estaria em emitir ainda mais CO2 para participar da conferência do clima. É verdade que aviões lançam carbono na atmosfera. Mas existem outras coisas muito piores em termos de mudança climática. Aço é uma delas.
Você não ouve ninguém fazendo comentários sarcásticos sobre geladeiras, carros, elevadores, metrôs e pontes, porque aço é uma das fundações do que entendemos por vida moderna.
O combustível queimado por aviões é responsável por cerca de 2% das emissões globais de gases de efeito estufa. Na siderurgia, esse número é quatro vezes maior.
O mundo consome por ano algo como 230 quilos de aço per capita (isso mesmo, 230 quilos para cada um dos 8 bilhões de seres humanos do planeta).
É díficil descarbonizar uma siderúrgica. O processo mais utilizado, em altos-fornos que queimam carvão mineral, libera enormes quantidades de dióxido de carbono.
Uma corrida tecnológica global está em curso para encontrar outras maneiras de transformar o minério de ferro em um dos materiais essenciais para o desenvolvimento e cuja demanda deve seguir aumentando a taxas de dois dígitos pelo futuro próximo.
O assunto interessa ao Brasil. O país é o nono maior produtor do mundo e um dos líderes na produção de eletricidade limpa, o insumo mais importante para produzir hidrogênio de baixo carbono – um dos caminhos mais promissores para a obtenção chamado “aço verde”.
Mas quem largou na frente foram os suecos.
Pioneirismo nórdico
Com financiamento da União Europeia, o consórcio sueco Hybrit – SSAB (siderúrgica), LKAB (mineradora) e Vatenfall (energia) – inaugurou em 2021 uma planta-piloto no norte do país.
Na mesma região, a H2 Green Steel tem ambições ainda maiores. Esta semana, a startup anunciou uma captação de US$ 4,9 bilhões, que se soma a outros US$ 2,1 bi já garantidos, para erguer a primeira usina de aço verde do mundo de escala comercial (na imagem acima).
A expectativa é que a companhia, que tem pouco mais de três anos de vida, comece a produzir em 2027.
Em vez do coque, um tipo de carvão fóssil essencial na fabricação do aço, a planta vai utilizar hidrogênio verde.
- Num alto-forno tradicional, o minério de ferro e o carvão são aquecidos a altíssimas temperaturas, gerando uma reação química que “purifica” o minério, removendo o oxigênio;
- O subproduto natural desse processo é o CO2, que é lançado no ar;
- Com o novo método, chamado de redução direta (DRI), o hidrogênio faz o papel do coque – e o que sobra é apenas vapor d’água.
Cada tonelada de aço produzida no processo convencional gera quase duas outras de dióxido de carbono. Na H2 Green Steel, o cálculo é que essa pegada climática fique em somente 50 quilos por tonelada.
Cerca de metade do volume de 2,5 milhões de toneladas anuais que a H2 Green Steel vai produzir já foi vendida em contratos de longo prazo com montadoras (Mercedes-Benz, Porsche e Scania) e seus fornecedores, como a alemã ZF Friederichshafen.
Sopa química
Em Woburn, uma cidadezinha a cerca de 20 km de Boston, outra startup encara o problema de um ângulo completamente diferente.
A Boston Metal, fundada por engenheiros do MIT e com o fundo de Bill Gates e a Vale entre seus investidores, está refinando os “caldeirões” em que pretende purificar o ferro usando apenas eletricidade – limpa, é claro.
A tecnologia da empresa foi batizada de eletrólise de óxidos fundidos. Trata-se basicamente de uma sopa de metais em que a reação química que purifica o ferro é induzida por uma corrente elétrica.
Não há combustível fóssil envolvido nem poluição atmosférica: o subproduto é apenas oxigênio. Os equipamentos de teste (na foto abaixo) ficam no mesmo edifício que abriga os escritórios da companhia.
O brasileiro Tadeu Carneiro, CEO da startup, afirma que o método tem uma vantagem importante em relação ao que usa hidrogênio verde. Primeiro, não é necessário produzir o gás.
Segundo, e talvez igualmente importante: a eletrólise funciona independentemente da qualidade do minério de ferro.
A redução com hidrogênio exige uma matéria-prima com uma concentração mínima de ferro, que não é produzida em qualquer lugar do mundo (a Vale é uma dessas fornecedoras).
A eletrólise da Boston Metal ainda não foi aplicada em escala. A primeira operação comercial deve ser inaugurada no primeiro trimestre deste ano em São João Del Rey (MG).
O objetivo não é produzir aço verde. A empresa vai instalar seus caldeirões eletroquímicos para extrair metais de alto valor de rejeitos de mineração. A técnica é a mesma que será usada em sua siderurgia do futuro.
A ideia é refinar ainda mais o processo, para que em 2026 seja montada uma unidade de demonstração da aplicação no aço.
Na última semana de janeiro, a empresa anunciou o aporte final de sua rodada série C, que totalizou US$ 282 milhões.
Outras avenidas
Pesquisadores da Universidade de Birmingham, na Inglaterra, desenvolveram um método que poderia cortar até 90% das emissões dos altos-fornos de uma siderúrgica convencional.
Usando cristais de perovskita, um material que contém nióbio e outros metais, o método recicla o CO2 emitido na produção do aço, usando-o como fonte de energia.
A ideia tem a grande vantagem de custar pouco, pois não há a necessidade de grandes adaptações nas usinas existentes. Mas os testes ainda não foram realizados fora do laboratório.
Este é o dilema da siderurgia, uma indústria essencial e poluente em igual medida. Muitos dos equipamentos em uso hoje ainda têm décadas de vida útil pela frente.
Fazer a transição para um modo de produção limpo vai custar centenas de bilhões de dólares – e vai levar tempo.
José Noldin, também brasileiro e CEO da francesa Gravithy, afirma que o caminho da siderurgia é mais claro que o de outros setores de difícil descarbonização.
“Temos tecnologias viáveis, e a legislação começa a ficar clara”, diz ele, em referência ao crescimento do mercado regulado pelo mundo e também a iniciativas como à sobretaxa europeia sobre produtos que embutem emissões.
E em geral o aço não está entre os itens mais caros dos produtos em que ele é utilizado. Isso significa que a cobrança de um prêmio verde não tem tanto impacto no custo final.
“Se você usar só aço verde, o carro vai ficar 200, 300 dólares mais alto. Em alguns outros setores descarbonizar significa duplicar, triplicar o preço.”