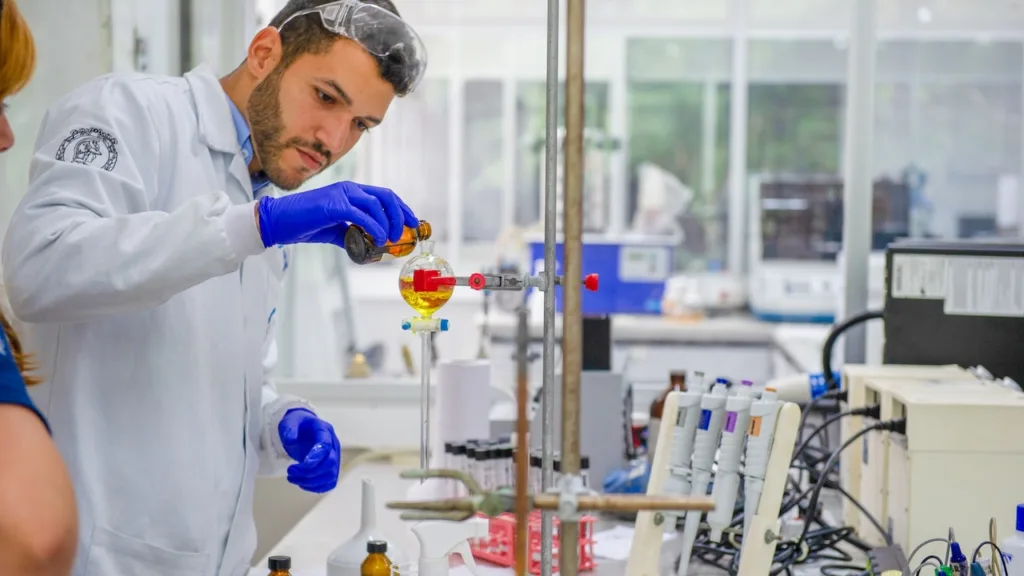
O que acontece com baterias de celulares, computadores, carros e outros eletrônicos quando perdem sua vida útil? Estima-se que apenas 5% delas são recicladas atualmente, consequência do descarte incorreto da maior parte dos equipamentos. E vão parar em lixões, o que aumenta o risco de incêndios e contaminação do solo. Atenta ao problema, a multinacional brasileira Tupy investiu em Pesquisa & Desenvolvimento (P&D) para criar uma solução para a reciclagem de baterias. Na fase atual do projeto, iniciado em 2021, está sendo construída uma planta-piloto.
Embora bastante tradicional no segmento de componentes estruturais para bens de capital — máquinas, veículos e equipamentos, nos últimos anos, a companhia tem investido em P&D de produtos, serviços e tecnologias que promovam a descarbonização. Até o momento, anunciaram operações de bioplantas — que geram energia limpa, combustível renovável e fertilizante organomineral a partir de resíduos de animais; motores movidos a biocombustíveis; pesquisas no uso do hidrogênio e, agora, a planta-piloto de reciclagem de baterias.
Esta operação contará com uma nova tecnologia, 100% nacional, desenvolvida em parceria com o LAREX — Laboratório de Reciclagem, Tratamento de Resíduos e Extração do Departamento de Engenharia Química da Escola Politécnica da USP (POLI-USP), de excelência internacional na área.
O projeto foi realizado em parceria com a Embrapii, empresa pública de fomento à inovação na indústria brasileira, e Finep, com investimento de cerca de R$ 12,3 milhões em pesquisas. Deste total, R$ 7 milhões foram aportados pela Tupy.
Primeira planta de reciclagem de baterias via hidrometalurgia flexível do país, ela funcionará no Instituto de Pesquisas Tecnológicas (IPT) com capacidade para processar mais de 300 toneladas de baterias anualmente, o que equivale a reciclar componentes de aproximadamente 800 veículos elétricos.
A nova tecnologia já tem três patentes registradas globalmente e é uma evolução dos processos de reciclagem existentes. O mais tradicional é chamado de pirometalurgiae consiste basicamente em queimar as baterias em um forno gigante — método relativamente simples, mas pouco eficiente e com maior impacto ambiental. A pirometalurgia não proporciona bons graus de pureza no material recuperado. “Na prática, o processo acaba funcionando mais como destino final das baterias do que servindo à reciclagem propriamente dita”, explica André Ferrarese, diretor de Pesquisa e Desenvolvimento Disruptivo na Tupy. Além disso, o processo tem alto consumo de energia e grande emissão de poluentes.
Já a hidrometalurgia utiliza processos químicos no lugar da queima, e envolve desmontagem das baterias e separação de seus componentes. Isso garante melhores taxas de recuperação dos minerais e maior grau de pureza. Os núcleos das células das baterias são separados de materiais, como cobre, alumínio e plástico, que seguem para suas cadeias próprias de recuperação. Em seguida, os núcleos são moídos e submetidos a um tratamento químico que permite separar os minerais que serão reutilizados em novas baterias.
A tecnologia a ser aplicada na planta-piloto da Tupy é um aprimoramento deste processo de hidrometalurgia, uma vez que permite a reciclagem conjunta de baterias com composições químicas diversas — as que são utilizadas em equipamentos eletrônicos e também as de veículos elétricos e bancos de bateria para armazenagem de energia solar e eólica, por exemplo. Por permitir essa mistura, a nova tecnologia é chamada de hidrometalurgia flexível.
“Essa flexibilidade é importante para a viabilidade econômica e a produtividade, pois permite reunir mais rapidamente o volume necessário de material para reciclagem”, explica Ferrarese. A hidrometalurgia flexível garante taxas de recuperação de minerais e pureza acima de 90%, ideais para a produção de novas baterias.
Reciclagem: solução limpa para déficit de lítio
A nova tecnologia é importante também para aumentar a disponibilidade de lítio, mineral essencial para a produção de baterias, sem a necessidade de abrir novas minas. Segundo a consultoria McKinsey & Company, a partir de 2030 haverá um déficit de até 20% na capacidade produtiva do mineral. “A reciclagem é fundamental para equilibrar esta cadeia de suprimentos porque a demanda por mais mineração não pode ser resolvida de forma ágil”, analisa Ferrarese.
Calcula-se que, para atender à demanda, até 2035 seriam necessárias 70 novas minas em operação para extração de lítio, além de cobalto e níquel, outros minerais estratégicos nessa cadeia. O tempo médio para entrarem em operação na escala adequada e com planos de proteção ambiental corretos é de 15 a 20 anos.
Além do longo prazo de implantação, há também o desafio de equacionar os impactos ambientais na atividade mineradora. Para produzir a quantidade de minerais críticos, como o lítio, para uma única bateria são necessários 26 mil litros de água e a movimentação de mais 225 toneladas de terra. Com minerais reciclados, a redução nas emissões de gases de efeito estufa (GEE) é de cerca de 70%. Por isso, a legislação europeia prevê que, até 2031, 80% das baterias devem ser recicladas.
No Brasil, o programa Mover também introduziu a importância da reciclagem dos veículos e, em sua regulamentação, poderá trazer mais clareza na definição das responsabilidades dos envolvidos em toda a cadeia produtiva.
Sobrevida para baterias de automóveis
Uma outra parceria firmada pela Tupy, desta vez com o Senai, avalia, já no início do processo de desmontagem das baterias, aquelas que podem ganhar uma segunda vida antes de passar pela reciclagem. “Muitas baterias de carros elétricos ainda têm entre 70% e 80% da sua carga”, diz Ferrarese. “Isso as inutiliza para mobilidade, pois ficam com tempo de autonomia significativamente reduzido em viagens. Mas, podem ser utilizadas para armazenamento de energia solar, por exemplo. O novo uso permite prolongar o tempo de vida da bateria por mais cinco a dez anos, o que é ótimo em termos de sustentabilidade.”